3Dプリンターの用途や使い道にはなにがある?特性やメリット、導入事例を紹介!
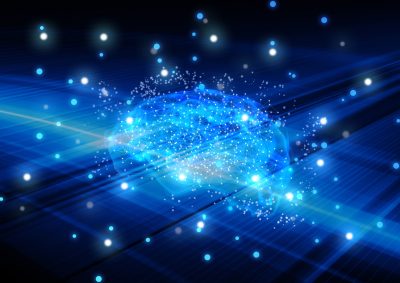
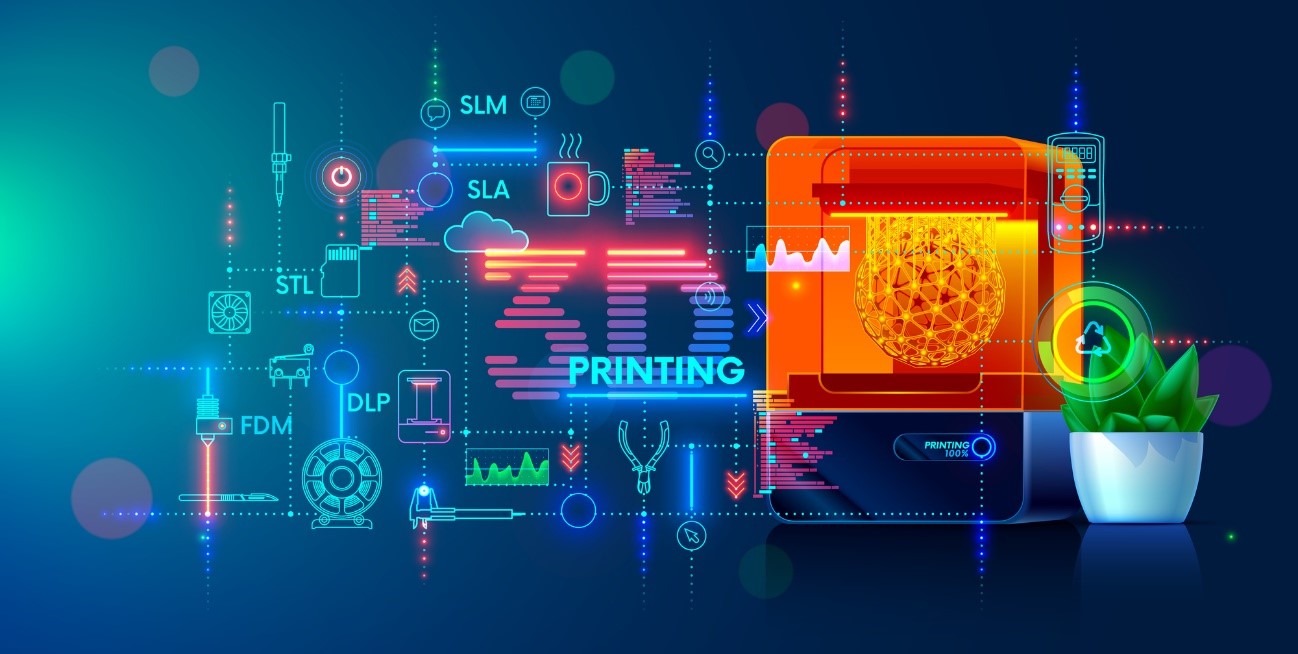
3Dプリンターが登場したとき、産業界に革新をもたらす技術だと大きく取りあげられ話題になりました。3Dデータをもとに立体的なものをプリントする3Dプリンターは、製造工程を簡素化できることから、さまざまな分野で活用に向けた取り組みが行なわれています。
とはいえ、革新的な技術である3Dプリンターも実際に触れる機会がないと、どのようなものが作られていて、どのように活用されているのかなど、使い道をあまり理解していない方も多いのではないでしょうか。
今回の記事では、3Dプリンターの特性や使用するメリット、使い方や導入事例などを紹介します。
3Dプリンターの特性
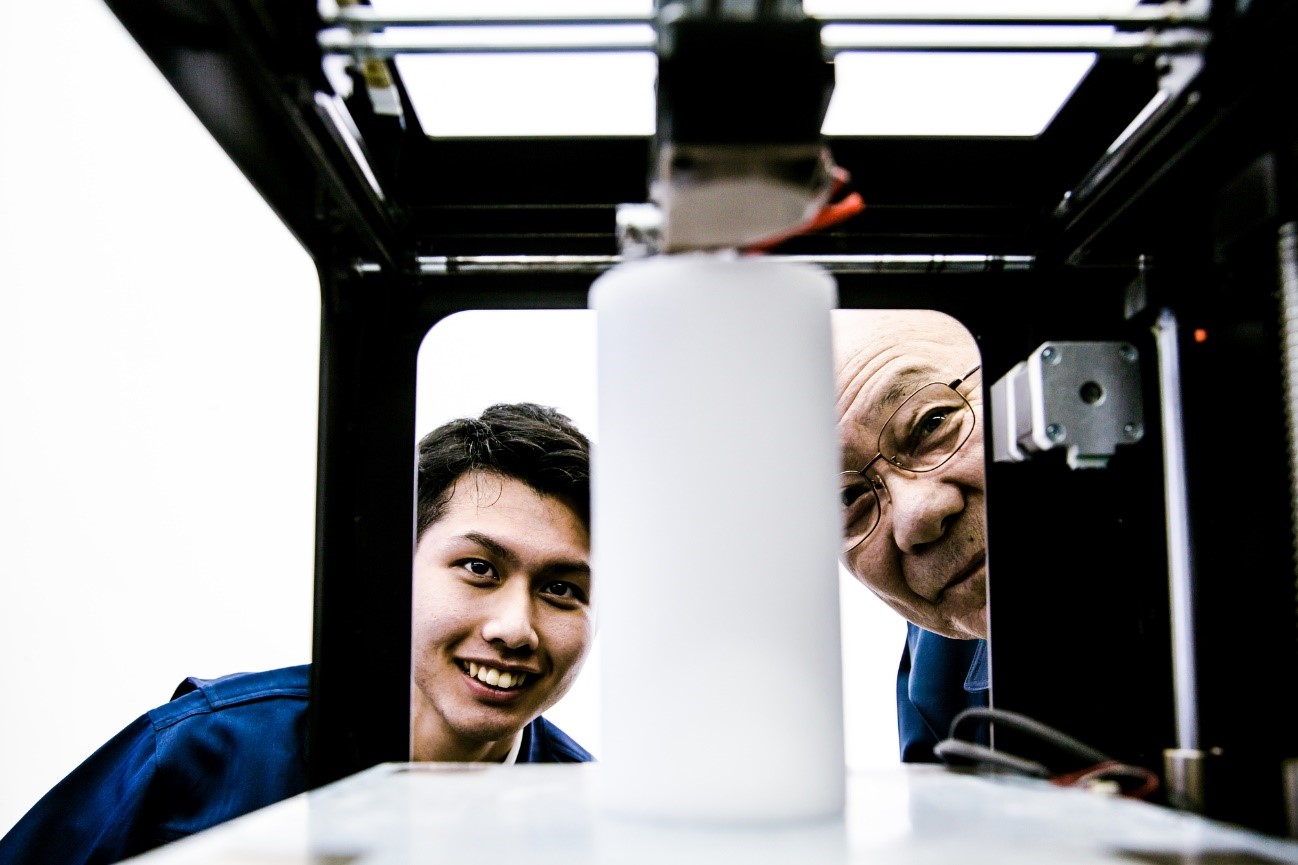
3Dプリンターは立体的なものをデータから作れる画期的な技術ですが、どのような形でも作りあげられるわけではありません。作りたいものをイメージし、3Dプリンターの用途や特性を把握したうえでものづくりを進めましょう。
3Dプリンターで用いる材料は多種多様
3Dプリンターは当初、ABS樹脂[作成者3]やPLA樹脂が使用されていました。最近では、耐候性・耐熱・耐薬品性に優れた素材や、摩耗性に優れ高温条件下でも機構部品として利用されるエンジニアリングプラスチックも使用できるようになりました。また、3Dプリンターではアクリル樹脂、熱可塑性ポリウレタン、金属なども使えるようになっています。
このように使用できる材料が増えたことから、多くの業種で3Dプリンターが導入されるようになりました。活用している業種は幅広く、製造業をはじめ、医療、建築、教育、自動車、フィギュア製造販売や宇宙・航空機業界にまで使い道が広がっています。
3Dプリンターの機種によって使用できる素材には限りがある
さまざまな素材を扱えるようにはなったものの、3Dプリンターの機種によっては、素材が1種類しか使えない機種もあります。このようなプリンターは多くの場合、いわゆるローエンド機種に分類されます。
これに対し、いわゆるハイエンド機種では、多種多様な材料を組み合わせて使えるものが少なくありません。幅広い用途での活用を検討する場合も、ハイエンド機種1台でカバーできる範囲は広くなったといえるでしょう。
ものづくりの時短を実現できる
これまでさまざまなものを作りあげる際、専門の業者に試作品を含めた製作の依頼をしていたため、完成までに時間も費用もかかっていました。
3Dプリンターを導入すると試作品を自社内で製作できるため、外注する際の費用や、コミュニケーションに費やす日数、試作品のできあがりを待つ時間を削減でき、ものづくりの時間や費用を圧縮できます。
ただし、3Dプリンターは3Dデータを読み込んでから、造形物が完成するまでに最低数時間、金属などの造形物によっては数十時間程度を要します。試作品の製作は時短が可能ですが、ある程度の数量の同じ形のものを製作すること(いわゆる量産)には向かないことに留意しましょう。
3Dプリンターを用いるメリット

実際に3Dプリンターを使用すると、どのようなメリットを享受できるでしょうか。おもなメリットとして、ここでは次の6つを解説します。
アイデアを簡単に具現化できる
立体的なものをデザインする際、3Dプリンターがなければ、金型を製作する前にイメージどおりかを何度もデータの状態でチェックする必要があります。1度金型を作ってから修正が必要になると、もう一度金型の費用がかかるからです。そのため、商品ができあがるまでに相当の時間を要します。
3Dプリンターで立体プリントができれば、実物に近いものをさまざまな角度から観察できます。組み合わせの変更や形状を変更するなど、新しいイメージやアイデアが生まれる機会も増えるでしょう。
開発期間・コストの削減を実現できる
3Dプリンターのない時代は、作品を作り終えるまでに金型を製作する必要がありました。それに対し、3Dプリンターは3Dデータさえあれば、そもそも金型の製作を外注しなくともよくなります。試作品やテストパーツ、治具なども自社内で容易に製作できることから、期間を大幅に短縮でき、費用も大幅にコストカットできるのです。
さらに、データやパソコンの画面だけでは気が付かないデザインミス・設計ミスを、金型の製作前にチェックでき、ミスを未然に防ぐことで無駄なコストを抑えられます。さらに、少量であれば実際の最終製品も3Dプリンターを活用すれば、さらにコストダウンが期待できるでしょう。
品質の向上を図れる
3Dプリンターを使えば実物と同じ形状でプリントでき、試作品を製作している段階で、形状や動作を念入りにチェックできます。また、部品の組立や事前検証も容易になるため、品質の向上も図れるでしょう。
ある一定のサイズまでは、3Dプリンターで製造することが可能です。パーツを一つひとつ組み合わせていたものも、一つのものとして設計を見直して製造することで、耐久性においても従来品より向上することが期待できます。
また、耐久テストも事前に行ないやすくなり、製品化後のトラブル発生リスクの抑制につながるでしょう。
切削では作れない形の造形が可能
3Dプリンターは、3Dデータをもとにして積層方式で物体を形成するため、細部が複雑な形状のものでも製作することが可能です。それに対し、切削加工はある程度の大きさがある材料に対して、工具を使って削り出す必要があります。形状が複雑だと1回では製作できず、手順を複数回に分けなくてはならないため、それだけ時間もかかってしまうでしょう。
切削でも加工ができる形状は多数ありますが、素材から大きく削る必要がある形状だと、削る時間と材料費が多くなりがちです。3Dプリンターなら、複雑な形状でも1回で造形できるため、製作時間の短縮だけでなくコスト削減も期待できるでしょう。
情報流出のリスクを防ぐ
従来であれば、試作品においても、金型などを含めた製作を専門業者に依頼していました。その際、外部に委託することで生まれる情報流出のリスクに備え、機密保持契約の締結など煩雑な手続きをする必要があったのです。
3Dプリンターを使用すれば、試作品の製作の内製化により、製品形状や製品データを外部に持ち出さなくて済みます。情報流出のリスクを防げる点もメリットといえるでしょう。
必要なときに、必要な場所で、必要なだけ製作できる
これまで、製品が故障した際には、あらかじめ予備の製品や金型を用意しておくことで対応していました。しかし、3Dプリンターを導入すれば、データが手元にあるため必要なときに製作できます。
変更や改良を加える場合でも、データを調整するだけで対応が可能です。金型の用意も不要で、商品の余剰在庫を抱える必要もありません。また、使用していたパーツが製造中止となった際、製造や修理ができないという悩みも解消されます。
データを送付するだけで製作でき、金型を遠方まで運んで製作するといった手間も省けるので、利便性と機動性が非常に高まります。
3Dプリンターの使い道・導入事例
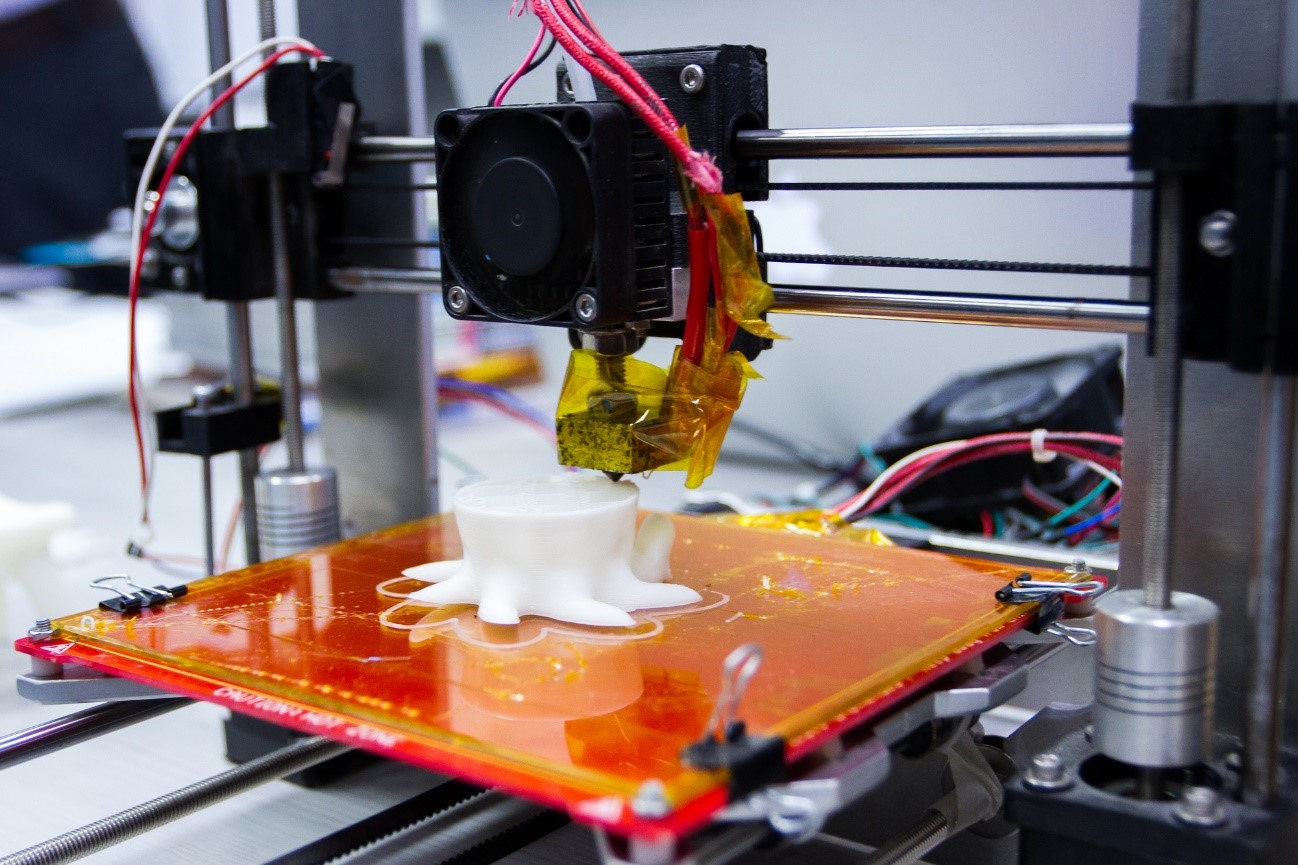
実際に、3Dプリンターはどのような使い道をされているのでしょうか。導入事例を業種別に紹介します。
製造業
製造業では、早い段階から3Dプリンターの導入が進んでおり、金型の製造などで活用されています。その他に、メンテナンスや作業の補助治具として使い道を広げている企業もあります。
また、試作品の製作に3Dプリンターを用いる企業も、少なくありません。例えば、家電メーカーで試作品製作に取り入れた場合、完成までに要する時間とコスト削減につなげることが可能です。
個人ユーザー
3Dプリンターはさまざまな種類がありますが、熱溶解積層方式の3Dプリンターは個人でも手に入りやすい価格帯です。そのため、近年では個人で利用するケースも増えてきました。
さまざまな研究機関や普段から3Dを扱っている個人ユーザーが3Dデータを発表し、それがきっかけとなって個人でグッズを製作する人も増加しています。これには、DIYへの関心の高まりも影響しているのでしょう。
なかには、携帯ホルダーや便利グッズなど、3Dプリンターを使って独自のデザインやアイテムを製作・販売することで、副収入を獲得する人も増えています。
教育関係
教育分野においても3Dプリンターの導入が進み、中学・高校・大学などの教育機関で使われています。
授業で取り入れる場合の使い道としては、生物や物体の構造を理解するためのツールとして使われたり、デザインの授業で立体造形物を取り扱ったりするなど、幅広く活用されています。
小学校の算数では、2次元でイメージすることが難しい円錐や三角錐、円などを立体にして説明することで、図形の苦手意識克服に役立っているようです。算数だけでなく、図画工作や美術でも有効活用されています。
思い描いたものが3Dで形になる体験をすることで、子供たちがものづくりへの興味関心を持つようになるでしょう。また、これまで平面でとらえていたものを立体的な造形物にすることで、理解力が向上するという効果も期待されています。
建築設計
建築設計では、建築模型の製作に3Dプリンターが活用されており、海外を中心に建築物そのものを製作する建設用3Dプリンターも活用が始まっています。海外では、住宅やオフィスビルの建築などで3Dプリンターが使われています。例えば、ベルギーでは巨大な3Dプリンターを使い、世界初の2階建て住宅を建築しています。
施工費用が安価で済むだけでなく、施工時間が圧倒的に短縮されて人が手を加える労力も格段に減少するので、材料費や人件費の削減も可能です。
日本は地震が多く、建築物の強度や使用する素材、工法はあらかじめ定められているので、3Dプリンターでの建築は難しいといわれています。しかし、3Dプリンターで使える材料を開発している日本企業が増えているため、日本でも建築の一部に取り入れられる日が来るでしょう。
医療関係
医療関係では、特に歯科医療や歩行補助具・治療用具の制作、手術前のシミュレーションなどで、3Dプリンターの活用事例が多数あります。
歯科医療の場合、総入れ歯の義歯の製作には相当時間がかかりますが、3Dプリンターを導入することにより、数時間での製作が可能です。入れ歯以外にも、被せものや詰めものなど、さまざまな歯科技工物が3Dプリンターを使って製作されています。一人ひとり違った形の歯科技工物をカスタマイズ生産できるため、海外で3Dプリンターの活用が最初に広まったのが歯科医療の分野です。
医療機器としては、特に医療インプラントといわれる人工骨(大腿骨、脊椎、骨接合材など)にも利用されています。また、医療用モデルとして脳・肝臓などの臓器を3Dプリンターで製作することで、手術で切る場所や腫瘍の取り出し方をイメージしやすい形で説明が可能です。
最近では、3Dプリンターでシリコン製の人工心臓を作る研究も進んでいるため、3Dプリンターで人工心臓が作られる日も、そう遠くないかもしれません。
玩具
安価な機種が販売されて家庭でも気軽に購入できるようになり、3Dプリンターを楽しむ人も増えてきました。すでに作成されたデータを入力すれば、子供用の玩具を製作するのも容易です。実際に、無料で配布されているデータをもとにして、立体パズルなどの玩具を制作している人もいます。
また、フィギュアも無料で3Dデータが配布されているものもあり、3Dプリンターを使えば短時間で製作が可能です。写真からミニチュア3Dフィギュアを製作するサービスもあり、3Dプリンターは積極的に活用されています。
航空宇宙業界関係
航空・宇宙業界では、金属材料や炭素材、高機能性樹脂材料など数多くの先端素材が使用されています。複雑な形状の部品も多いので、複雑な形状のものでも製作可能な3Dプリンターとは相性が良いようです。
すでに最大手の航空機メーカー製の機材に登載されている新型エンジンには3Dプリントされた部品が300点以上も使用されています。別の大手航空機メーカーでも、客室内などの内装部品や翼の下の支柱部分などの製作に使用され、機体部品の製作に使われるケースも増えてきました。
エンジン部品を3Dプリンターで製作することで、開発から製作にかかる費用の削減や製作期間の短縮、さらにはメンテナンスでの効率化が実現できるでしょう。
今後3Dプリンターの需要は高まっていく
今後、3Dプリンターの需要は高まり続ける見込みです。ただ、3Dプリンターの造形方法の技術革新が進んだことにともない、用途によって最適な造形方式が選択されていくことでしょう。
新型コロナウイルスの感染拡大により、3Dプリンターを購入し、自宅で個人用グッズを製作するユーザーや、小さな子供向けの玩具やパズルを自作する家庭が増えてきました。
3Dプリンターは、製造業での導入は進んでおり、製造業で使用する工作機械の位置付けになりつつあります。最終製品の製造に限らず、試作品や治工具を製作する際に3Dプリンターの使用に切り替えるなどしており、業種ごとの3Dプリンター導入は着実に進んでいるといえるでしょう。
ただし、3Dプリンターには課題もあります。例えば、造形に時間がかかり大量生産には不向きなことや、まだ新しい製法のため使用する箇所によっては品質などの面から法的な規制をクリアする必要があることなどが挙げられるでしょう。
まとめ
3Dプリンターは製造業をはじめ、会社から個人まで幅広く利用されています。3Dデータをもとにして立体的に物体を製作できる多様性から、多くの業種や分野でも導入が進められています。
物体の造形方法や使用する材料によって効果の程度は異なりますが、この技術がさらに発展した場合、製品の開発にかかる時間やコストの削減に加え、製作にかかる材料費や人件費、輸送費などのトータルライフサイクルコストの削減が期待できるでしょう。
ただし、現在の3Dプリンターは製作に時間を要するため、製品そのものを大量生産することには不向きです。実際、国内の製造業でも金型や試作品を短期間で製作する工作機械の一部という立ち位置からは脱却できていません。
とはいえ、3Dプリンターの開発はどんどん進んでいます。親和性の高い医療現場へは積極的に導入されているため、人工心臓や内臓が3Dプリンターで作られるのも、そう遠い未来ではないのかもしれません。
今後、3Dプリンター市場が拡大し、より多くの人が気軽に使えるようになる可能性もあります。使い道が広がりゆく3Dプリンターに、ますます注目が集まることでしょう。