仮焼結しない? 新タイプの電子ビーム金属3Dプリンター(英・Wayalnd Additive)
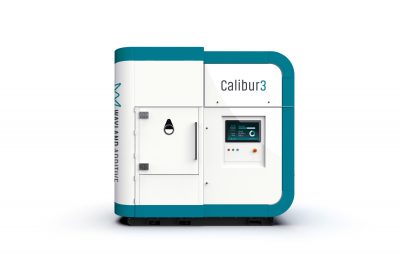
目次
パウダーベッド/電子ビーム方式(EB-PBF)の金属3Dプリンターとは
そもそもパウダーベッド方式とは
パウダーベッド(パウダーベッドフュージョン=粉末床溶融結合)方式の金属3Dプリンターは、専用の金属プレート上に敷き詰めた金属粉末を、ワークのスライス断面に沿って溶融・凝固させます(ワークの形状によっては応力除去、変形防止のためサポート材を付ける必要があるため、その際はサポート部分も溶融・凝固させる必要があります)。
この溶融・凝固が一通り完了すると、プレートが一段下がり、その上に新たに金属粉末を敷き詰め、ワークの断面に沿ってまた溶融・凝固→プレートが一段下がる→新たに金属粉末を敷き詰める。
この過程をワークの造形が完了するまで繰り返します。
電子ビーム方式(EB-PBF)とは
電子ビーム方式の金属3Dプリンターでは、専用の金属プレート上に敷き詰めた金属粉末を溶融するエネルギー源として電子ビームを使用します。
金属粉末に電子ビーム(マイナス電荷)をそのまま当ててしまうと、金属粉末が帯電し、粉末同士が反発しあって拡散→スモーク現象が発生することで正常な造形ができなくなります。
そのため、溶融・凝固のプロセスの前に粉末全体を仮焼結させるまでヒーティングを行います。
全体を仮焼結させてからワークの断面に沿って電子ビームを当て、溶融・凝固させます。
電子ビーム方式(EB-PBF)装置メーカーについて
これまで世界で使われている電子ビーム方式の金属3Dプリンターは、スウェーデン発祥で現在はGE Additive傘下のArcam社のほぼ独占状態にありましたが、最近では国内メーカーも新たな装置を市場に参入しています。
仮焼結させない/Wayland Additive社の電子ビーム方式
上記で説明したように、通常の電子ビーム方式の金属3Dプリンターでは金属粉末全体を仮焼結させてから溶融・凝固するのですが、このWayland Additive社の電子ビーム方式(NeuBeam)では、粉末全体を仮焼結するのではなく、ワークの断面部付近とサポート部分のみに限定して仮焼結させるようです。
これによるメリットは、
- 粉末全体ではなく、該当箇所だけを仮焼結させれば良いため、造形時間の短縮が期待できる。
- レーザー方式(L-PBF)の金属3Dプリンターと同様に、造形完了後にワークおよびサポート以外の金属粉末はサラサラした状態のままということになり、造形後の粉末回収作業が楽になる。**
通常の電子ビーム方式と同様に、造形は真空中で行われるため、粉末酸化のリスクは最小限に留めることができます。
また、仮焼結させない焼き鈍し(アニーリング)程度の温度下で造形が行われるため、造形後の応力除去のための熱処理も必要ないようです。
一言でまとめると、電子ビーム方式とレーザー方式の金属3Dプリンター、それぞれの良いところを採用したような感じでしょうか。
**電子ビーム方式の粉末回収作業(=仮焼結体の除去)に関してはこちらも参照下さい。
使用する粉末粒径
一般的にレーザー方式の金属3Dプリンターに使用する金属粉末の粒径は15~45µm、電子ビーム方式の場合は45~105µmになり、それぞれの方式で造形しようとする場合、異なる粒度分布の金属粉末を準備する必要があるのですが、このWayland Additive社の電子ビーム方式 – Calibur3に使用する粒径は基本的にどちらも使用できるとのこと。
これはつまり、レーザー方式と電子ビーム方式両方の金属3Dプリンターを運用している企業にとっては、粉末管理を一本化できることになり、享受できるメリットは非常に大きいです。
<補足説明>なぜ、電子ビーム方式の粒径は(レーザー方式と比べて)大きいのか
上記で説明したように、電子ビーム方式で造形した直後のワークは仮焼結体で覆われた状態になっています。こちらをPRS(Powder Recovery System)という付属の装置で、圧縮空気を噴射することで仮焼結体を砕くのですが、この際、粉末粒子同士の衝突による発熱や、静電気の発生により、粉末粒子が小さい場合は粉塵爆発が発生する危険性があります。
電子ビーム方式で粒子径の大きな粉末を使用する理由は、この粉塵爆発のリスクを回避するためです。
NeuBeamプロセスを搭載したWayland社のCalibur3
上記で説明したNeuBeamプロセスはWayland Additive社のCalibur3に搭載され、2021年の秋頃から出荷を開始するようです。

造形領域としては、300 x 300 x 450 mm (幅x奥行x高さ)ですが、後にリリースを予定しているCalibur4では450 x 450 x 450 mmになるようです。
Calibre3紹介動画
第一弾として、カナダの顧客に販売が決まったようです。
Wayland Additive Sells Electron Beam Metal 3D Printer to First Customer
より詳細な情報が発表され次第取り上げる予定です。
金属3Dプリンターによる試作・量産の見積依頼、DfAM支援サービス、お問合せ等はこちらから。