新アルミ合金について
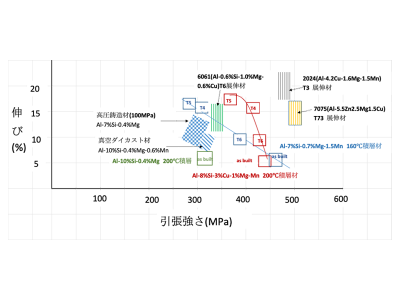
新しい金属3Dプリンター用アルミニウム合金
金属3Dプリンター総合技術サービスを提供する当社では、(株)コイワイ、東洋アルミニウム(株)、九州大学、千葉工業大学が開発した新しい金属積層用アルミニウム合金粉末に関し、特許実施契約に基づいて、3D造形による新たな用途への活用に取り組んでいます。
1.高強度アルミ合金(Al-Si-Mg-Mn系)<日本特許 6393008、中国特許、米国特許>
金属3Dプリンターで使用されるアルミニウム合金においては、Al-10%Si-0.4%Mg合金が広く知られています。
積層造形時に基盤プレートを予熱しない場合、450MPa程度強度を示しますが、同合金で歪みを生じないように造形するためには、積層造形時の基盤プレートの温度を200℃近くに保持する必要があり、強度は300MPa程度まで低下してしまいます。
(強度低下の理由として、200℃においてMg-Siの過時効組織が発生するためと考えられます)
一方、Mnを添加した新開発合金では、積層材のままでは400~500MPa程度(7000系合金レベル)の高い引張強度を示す。積層造形した製品の残留応力を低減するためには、T5(300℃人工時効)、T4(535℃→W.Q.)、T6(535℃→W.Q.→人工時効)を行うことは有効である。
強度データについてはこちらのコラム記事も参照下さい。
化学成分 (%) | |
---|---|
Si | 7 |
Mg | 0.7 |
Fe | ≦0.3 |
Mn | 1.5 |
AI | bal. |
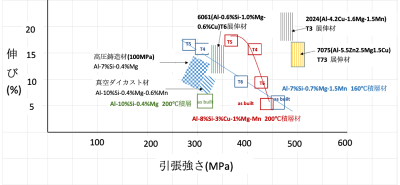
2.高強度アルミ合金(Al-Si-Cu-Mg-Mn系) <日本特許 6393008、中国特許>
CuとMnを含む合金は、1の合金よりも高い強度と伸びを示すことが可能です。熱処理の条件を選択すれば、各種の特性を得ることができます。
3.耐熱合金 <日本特許 6393008、中国特許>
鋳造用の耐熱アルミ合金としてJIS AC8A合金(Al-12%Si-1%Cu-1%Mg-1%Ni)が良く知られています。しかし、同合金を金属3Dプリンターで造形すると、むしろ従来知られている高温強度が得られません。
これを改善するため、遷移金属を添加した合金を用いることで、従来比1.5~2.0倍の値を示すことが確認されました。造形に際しては、レーザー方式の金属3Dプリンターを用い、従来行われるT6処理(510℃溶体化処理⇒水焼き入れ⇒焼き戻し)を行う必要はありません。
化学成分 (%) | |
---|---|
Si | 7 |
Mg | 0.7 |
Fe | ≦0.3 |
Mn | 1.5 |
AI | bal. |
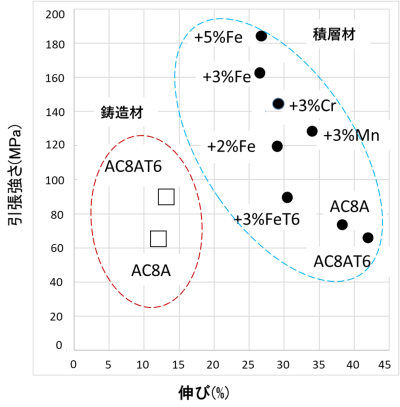